Exploring the Function of Jewellery Grinders in Gemstone Crafting
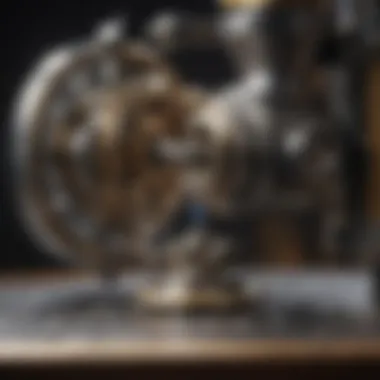

Intro
The world of gemstones is one that captivates the imagination with its vibrant colors and remarkable intricacies. Each stone is unique, possessing qualities that make it desirable for various applications, particularly in the realm of jewellery crafting. However, transforming a raw gem into a stunning piece of jewellery is no easy feat. It requires skill and precision, with jewellery grinders playing a vital role in this art. Understanding these tools, their mechanics, and how they impact the overall creation process is essential for anyone keen on delving deeper into the craft.
Gemstone Overview
Definition and Origins
Gemstones have fascinated humans for thousands of years. Essentially, they are pieces of mineral crystals that can be cut and polished into stunning objects of art. The origins of these beautiful stones date back to ancient civilizations, where they were not only used for adornment but also held significant spiritual and cultural value. Every culture that encountered gemstones breathed life into their legends, often attributing mystical powers to them. For instance, the ancient Egyptians valued lapis lazuli for its deep blue hue and believed it symbolized the heavens.
Historical Significance
The historical relevance of gemstones is vast. From the crowns of royalty adorned with sparkling diamonds to the talismans worn by shamans, these stones served various purposes through the ages. In many societies, gemstones were seen as symbols of wealth and status, treasured as a means of displaying power. The famous Hope Diamond, with its checkered history, offers a glimpse into how gemstones can influence people's lives dramatically. Moreover, gems have also played a significant role in trade routes, impacting economic landscapes significantly throughout history.
Gemstone Properties
Hardness and Durability
When it comes to gemstones, one of the most critical properties is hardness. Measured on the Mohs scale, this determines how resistant a stone is to scratching. For example, diamonds, rated a 10 on this scale, are practically indestructible and are preferred for engagement rings because they can withstand everyday wear.
It is crucial to consider the durability of a stone — not just its hardness but also how resistant it is to chipping or breaking. Softer stones like opals may require extra care due to their vulnerability, while harder stones like sapphires can endure much harsher treatment.
Color and Clarity
Color is perhaps the most immediately recognizable quality of a gemstone. Different stones display a wide range of hues, influenced by their chemical composition and structural characteristics. For instance, rubies are celebrated for their rich red tones, while emeralds are sought after for their alluring green shades.
Clarity, on the other hand, plays a substantial role in determining a gem's quality. Clarity refers to how clear a gemstone is, evaluating the presence of inclusions or blemishes that can detract from its overall beauty. A more transparent stone is generally more desirable. Understanding these properties not only helps in choosing the right stones for jewellery but also confirms how effectively a jewellery grinder can enhance these natural attributes.
"The alchemy of transforming a rough stone into a polished gem is nothing short of magical. Each grind brings it closer to its final brilliance."
Prolusion to Jewellery Grinding
Jewellery grinding sits at the crossroads of artistry and tradition, playing a crucial role in the crafting of exquisite gemstones. This section lays the groundwork for understanding how, at its heart, jewellery grinding isn’t just a mechanical process but a delicate dance of skill and creativity that transforms raw stones into breathtaking pieces of art. Emphasizing the journey from unpolished rock to polished gem, we aim to shine a light on the nuanced techniques and methodologies employed throughout history.
The Evolution of Grinding Tools
Over the centuries, grinding tools have journeyed through various transformations, each iteration marking a significant leap in the capabilities of gemstone crafting. In ancient times, artisans utilized rudimentary stones and abrasive materials to hone their craft, often employing methods passed down through generations. This human touch imbued each piece with a story, a folklore if you will, that celebrated the craftsmanship involved.
The first known tools for grinding gems can be traced back to the Egyptian civilization, where lapidaries made use of handheld devices, grinding gemstones against various surfaces to achieve desired shapes and finishes. Moving through history, the Middle Ages saw the advent of powered grinding wheels, which provided greater speed and precision, revolutionizing how gemstones were fashioned. By the time the Industrial Revolution rolled around, innovations in machinery allowed for mass production, changing the landscape of gemstone crafting forever.
As we sailed into the 21st century, the emergence of computerized grinding machinery has further refined the process. Tools equipped with state-of-the-art diamond blades enable precise cuts and finishes, allowing artisans to create intricate designs with unmatched efficiency. Thus, the tools of today are a marvelous blend of ancient wisdom and modern technology, showcasing how evolution is a constant theme in the realm of jewellery grinding.
Importance of Grinding in Gemstone Crafting
Grinding is not merely about achieving a glossy finish; it holds paramount importance in the overall jewellery-making process. Essentially, it’s about bringing the raw potential of a gemstone to fruitation, unveiling its inherent beauty and brilliance. An unground gemstone lacks the character and allure that a skilled grinder can unveil.
The importance of grinding can be boiled down to several key points:
- Quality of Finish: The grinding process significantly impacts the clarity and brilliance of the gemstone. A well-ground gem reflects light in a captivating dance, while a poorly finished one may appear dull.
- Shape and Structure: Achieving the intended shape of the stone is vital. Grinding allows artisans to sculpt such details with precision, ensuring that each gem fits within the designed piece perfectly.
- Durability: Proper grinding techniques can enhance the durability of a gemstone. By carefully polishing edges and surfaces, the likelihood of chipping or breakage during everyday wear is minimized.
As such, understanding the role of a jewellery grinder helps you appreciate how craftsmanship elevates a gemstone from mere rock to a treasured item of beauty. The nuances of grinding and polishing are what distinguishes mediocre pieces from truly exceptional works of art. Jewellery grinding is not merely a task; it's an art form, and understanding its significance is essential for anyone deeply engaged in jewellery making or collecting.
"Craftsmanship is about doing something with integrity and dedication, resulting in something that carries the maker's mark."
Types of Jewellery Grinders
Understanding the various types of jewellery grinders is essential for anyone dabbling in the craft of gemstone processing. Each type presents its own unique benefits and considerations, shaping how artisans can approach their work. Whether a jeweller is looking for efficiency, traditional craftsmanship, or superior cutting power, the choice of grinder plays a crucial role in not just the outcome of a piece but also the overall experience of crafting it.
Electric Grinders: Efficiency and Precision
Electric grinders often serve as the backbone of modern gemstone crafting. These machines are designed to maximize efficiency, allowing a jeweller to tackle multiple projects in a fraction of the time it would take using manual methods. One distinctive feature of electric grinders is their ability to maintain a steady speed, which provides a more uniform grind on the stone.
The benefits don’t stop at speed. Precision is another cornerstone of electric grinders. A jeweller can adjust settings to incredibly fine specifications, enabling detailed work on intricate designs. This flexibility means that whether one is working on a sparkling diamond or a more delicate gemstone, the outcome is usually consistent with high aesthetic values.
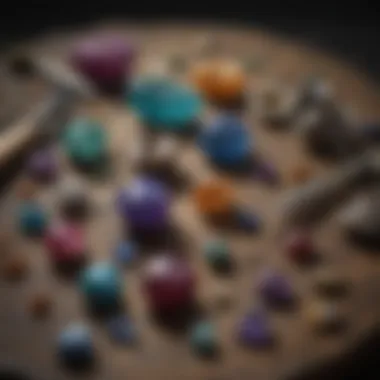

One might encounter a few drawbacks, though. Initial investment in electric grinders can be significant. Moreover, reliance on electricity means one must have access to power sources which isn’t always feasible in remote craft areas. Nevertheless, for those serious about their craft, the advantages often outweigh these considerations.
Manual Grinders: Tradition Meets Craftsmanship
On the flip side, manual grinders represent a deep-rooted tradition in the world of jewellery making. Often seen as a bridge between the craftsman’s hands and the tools of the trade, these grinders allow for an intuitive and tactile crafting experience. When a jeweller employs a manual grinder, they feel the stone and can respond to its nuances.
The charm of working with manual grinders lies in their simplicity and straightforward design. Without the distraction of electricity, the artisan can enter a meditative state, focusing solely on their craft. Furthermore, these tools often come with a lower price point, making them accessible for newcomers looking to test the waters.
However, there are challenges. Crafting with manual equipment generally demands more physical effort. The level of precision can also vary, depending on the skill of the artisan and their experience with the tool. For many, the trade-off is worth it, enabling a unique connection with each gemstone that electric grinders sometimes lack.
Diamond Grinders: Superior Cutting Power
When it comes to cutting power, diamond grinders take the crown. With their grinding wheels embedded with diamond particles, these machines are unmatched in terms of the surface finish they produce on even the toughest materials. Ideal for hard stones like sapphires and rubies, diamond grinders facilitate a smooth and efficient grinding process.
Much like electric grinders, diamond grinders often feature adjustable settings, allowing for tailored grinding sessions based on the specific needs of the gemstone. This adaptability enables jewellers to embrace a variety of projects without switching between multiple tools.
However, it’s essential to consider the cost associated with diamond grinders; they tend to be pricier than traditional options. That said, for individuals or businesses committed to frequently working with harder stones, these tools can prove to be a worthy investment. After all, in the world of gemstone crafting, the power of the tool directly correlates to the beauty and craftsmanship of the final product.
"Investing in the right grinder is not just a purchase, it’s a commitment towards the art of jewellery making."
Mechanics of a Jewellery Grinder
When one explores the world of gemstone crafting, understanding the mechanics of a jewellery grinder becomes crucial. This isn't just about having the right tool; it’s about recognizing how the components work together to achieve the desired outcome in jewellery making. The grinder operates as the backbone of the shaping and finishing process, and its mechanics influence both the quality and efficiency of crafting beautiful pieces.
Understanding the Grinding Wheel
The grinding wheel is perhaps the most critical part of the jewellery grinder. This wheel, often made from a mix of abrasive material, is where the magic happens. Its design plays a vital role in determining the effectiveness of the grinding process. There are different types of wheels suited for various applications—from rough shaping to polishing. For instance, a heavier grit wheel handles initial cuts and shapes, while finer grit wheels focus on smoothing and refining.
Key considerations regarding grinding wheels include:
- Material Composition: Different materials like aluminum oxide or diamond allow for diverse applications, influencing the outcome directly.
- Grit Size: This impacts how aggressively the wheel removes material. Coarser grits for rough cuts and finer grits for a finish.
- Balance and Shape: An unbalanced wheel can lead to uneven grinding and potentially damage both the grinder and the gemstone.
Understanding these elements not only aids in selecting the right wheel but also ensures that the grinder operates at optimal performance, allowing for better craftsmanship and quality results.
Motor Specifications and Their Impact
The motor specifications of a jewellery grinder significantly affect its overall functionality. A grinder’s motor is the powerhouse that determines the rotational speed and torque available for grinding. While it might sound technical, the importance boils down to practical implications for the gem cutter.
Factors to ponder about motor specifications include:
- Horsepower (HP): Higher HP motors can handle tougher materials and thicker stones. This is essential for both durability and longevity of the machine.
- RPM Ratings: The revolutions per minute rating dictates how fast the wheel can turn. This is particularly crucial when a specific speed is needed for certain types of grinding.
- Type of Motor: Whether an AC or DC motor can determine the versatility and control over the grinding process.
A well-chosen motor directly relates to efficiency during crafting. Going for a low-quality motor might save money upfront but can lead to frustration and poor craftsmanship in the long run.
"Understanding the mechanics behind your jewellery grinder can transform your approach to gemstone crafting, pushing your creations to new heights."
Grasping the mechanics of a jewellery grinder not only enhances technical skills but also deepens appreciation for the intricate art of gemstone crafting. With a firm foundation in wheel types and motor specifications, jewellers can equip themselves for any creative challenge that arises.
Techniques for Effective Grinding
The art of grinding gemstones is as much about finesse and technique as it is about the tools used. Understanding the correct methods can be a game-changer in the jewellery crafting process. By refining grinding techniques, artisans not only enhance the beauty of their creations but also optimize the lifespan and durability of the stones. Both new and seasoned jewellers should pay attention to these intricate methods, as they can make the difference between a mediocre piece and a stunning masterpiece.
Adjusting Speed and Pressure
When it comes to grinding gemstones, the right balance of speed and pressure is critical. Accelerating the grinder too quickly might lead to uneven surfaces, while too little pressure can result in a lackluster finish. Here are some key aspects to consider:
- Speed Control: Most grinders come with variable speed settings. Slower speeds are typically better for delicate stones. Adjusting the speed can also help in achieving the desired texture. You want to ease into a comfortable rhythm rather than blasting through the work.
- Pressure Application: Applying the correct amount of pressure helps in achieving a smooth finish. Too much pressure can cause chipping or cracking, particularly in softer gemstones like opals or pearls. It's vital to find that sweet spot where the stone is being shaped effectively without risking damage.
- Material Dependence: Different types of gemstones respond uniquely to speed and pressure. For instance, harder stones such as diamonds may require more aggressive techniques, while softer stones need a gentler touch. It’s often wise to consult material-specific guidelines to get the best results.
"Adjusting speed and pressure can turn a rough stone into a brilliant jewel. The finesse of the craftsman comes through in every deliberate touch."
Preventing Overheating of Stones
One major concern when grinding gemstones is overheating. Excessive heat can compromise the structural integrity of a stone, leading to fractures or even breakage. Here are some simple strategies to avoid overheating while grinding:
- Cooling Methods: Water can be used as a coolant. Applying a small amount of water to the stone while grinding helps in dissipating heat. However, be cautious not to over-saturate, as much water can make your work messy and wet.
- Short Intervals: Rather than grinding continuously, consider taking breaks. Grinding in intervals allows both the stone and the grinder to cool down, reducing the risk of heat build-up.
- Tool Maintenance: Keeping your grinding wheels in top notch condition ensures they operate at optimal levels. Dull wheels generate more friction, which can produce heat. Regularly checking and replacing worn wheels mitigates those risks.
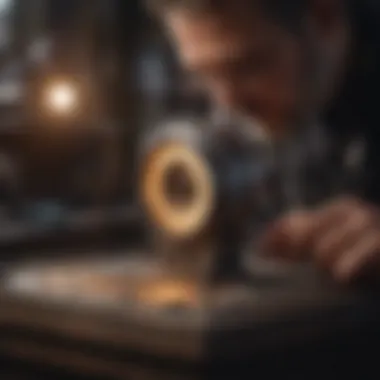

Incorporating these techniques into your gemstone grinding process not only elevates the quality of your final product but also ensures you’re respecting the beauty and integrity of the gems you work with. Understanding the nuances of speed, pressure, and temperature control form the backbone of effective grinding, making it essential for every jewellery maker.
Maintaining Your Grinder
The efficacy of a jewellery grinder directly impacts the quality and precision of gemstone crafting. Like any other tool, neglecting the maintenance of a grinder can lead to subpar results, which ultimately affects the final product. The importance of keeping your grinder in tip-top shape cannot be overstated; it’s akin to a chef using a dull knife – it makes the task harder and can compromise safety. Thus, regular maintenance ensures prolonged tool life, optimal performance, and, importantly, the integrity of the gemstones being worked on.
Regular Cleaning Tips
Cleaning is fundamental. Dust, debris, and remnants from gemstones can accumulate on the grinder, hampering its function. Regular cleaning protects the machine's motor and grinding wheel from unnecessary wear and tear. Here are some straightforward steps to follow for effective cleaning:
- Turn Off and Unplug: Always ensure the machine is off and unplugged before any maintenance work begins.
- Use a Brush: A soft brush is ideal for removing dust and residue from hard-to-reach areas.
- Wipe Surfaces: A damp cloth can be used to clean both the exterior and interior surfaces, ensuring no moisture gets trapped near electronic components.
"A clean grinder is as vital as a sharp blade to a chef; both are fundamental to achieving excellence in their craft."
- Inspect for Wear: While cleaning, take a moment to inspect for any signs of wear on the grinding wheel.
- Check Dust Collection: If your grinder has a dust collection feature, ensure it’s emptied regularly to allow for efficient operation.
Regular maintenance isn't just about keeping the grinder clean; it’s a proactive step toward achieving flawless gemstones and a seamless crafting experience.
Replacing Grinding Wheels: When and How
Like the blades of a well-used knife, grinding wheels will eventually wear down. Recognizing when to replace these wheels is crucial. As a general guideline, replacement is necessary when:
- You notice a significant decrease in grinding efficiency.
- There’s visible damage, like cracks or chips.
- The surface texture becomes uneven or glazed.
When it comes to replacement, the process is straightforward but must be done with care:
- Unplug the Grinder: Safety first! Ensure it is disconnected from power.
- Remove the Old Wheel: Follow the manufacturer's guidelines. This usually involves loosening a bolt or lever.
- Clean the Spindle: Before attaching the new wheel, clean any debris from the spindle.
- Install the New Wheel: Position it correctly, ensuring it's seated firmly, and tighten it securely.
- Test Run: Once reassembled, do a brief test run to ensure everything is working smoothly.
By keeping an eye on these vital aspects of maintenance, a jewellery grinder remains an efficient ally in the art of gemstone crafting.
Safety Protocols in Grinding
When it comes to jewellery crafting and gemstone grinding, safety isn’t just a suggestion; it’s a necessity. Crafting stunning pieces with gemstones can be a delicate procedure and oftentimes hazardous. Whether you're working in a small workshop or a larger studio, adhering to proper safety protocols can protect you from injuries and enhance your overall craftsmanship. Let's delve into why these protocols are crucial and how they can aid jewelry makers in their artistic journey.
Protective Gear: What You Need
The right protective gear is a cornerstone of safe grinding practices. Think of this gear as your first line of defense. Each piece serves a unique purpose, shielding you from flying debris and potential accidents. Here are essential items that should be part of your arsenal:
- Safety goggles: Protect your eyes from shards that can become airborne during the grinding process. It’s vital to keep those peepers safe from unexpected projectiles.
- Dust mask or respirator: Gemstones can release fine particles when ground, which aren’t good for your lungs. A proper dust mask or respirator can filter out harmful dust, ensuring you breathe easy.
- Heavy-duty gloves: While these won’t protect against everything, they provide a barrier against cuts from sharp stone edges.
- Ear protection: Grinders can be loud. Prolonged exposure can lead to hearing damage. Investing in earmuffs or earplugs is a wise move.
By using these items, you’re equipping yourself to face the demands of grinding with more confidence and less fear.
Preventing Dust Accumulation
Dust accumulation is more than an annoyance; it’s a health hazard. Fine particles not only cloud your workspace but can also pose serious respiratory dangers over time. Here are some simple strategies to keep your environment clean and minimize dust:
- Use a wet grinding method: When applicable, using water to cool the grinding wheel and stone can help significantly reduce dust. The water catches the particles, preventing them from settling in your workspace.
- Regularly clean your workspace: Make it a habit to clean your area after each session. A quick sweep or vacuum can do wonders. Ensure you’re using a vacuum with a HEPA filter designed to handle fine particles.
- Invest in dust collection systems: If your budget allows, a more permanent solution is a dedicated dust collection system. These machines can help keep the air clean while you grind.
"By taking care of dust accumulation, you not only protect your health but also maintain a more efficient workspace."
By prioritizing safety protocols, especially regarding protective gear and dust management, gemstone grinding becomes a safer, more enjoyable process. These practices not only safeguard your well-being but also enhance your ability to create exquisite jewellery designs. After all, a safe artist is a productive artist.
The Future of Grinding Technology
The horizon of grinding technology is ever expanding, promising to reshape how gemstones are crafted. As the demand for high-quality, precision-cut gems increases, so does the need for advanced grinders that can meet both the technical and artistic needs of jewellery makers. This section delves into groundbreaking innovations and the burgeoning impact of automation in the art of gemstone crafting.
Innovations in Grinding Equipment
In recent years, various advancements have emerged in the realm of grinding equipment. One stellar innovation is the computerized numerical control (CNC) grinders, which offer unparalleled precision. With CNC machines, artisans can input detailed designs, ensuring that even the most intricate cuts are replicated accurately every time. This technology significantly reduces the margin for error, making the crafting process smoother and yielding a higher quality final product.
Furthermore, the introduction of state-of-the-art diamond grit tools has revolutionized the cutting process. These tools not only enhance efficiency but also provide cleaner cuts, maintaining the integrity of the gemstone's original beauty. The advancements in diamond-coated wheels allow for greater versatility in grinding diverse materials, be it the delicate nature of opals or the sturdiness of sapphires.
Another exciting development is the integration of 3D printing technology in the grinding process. Artisans can now prototype their designs, transforming virtual models into tangible, workable forms. This not only saves time but also allows for rapid experimentation, leading to unique and personalized pieces that stand out in a saturated market.
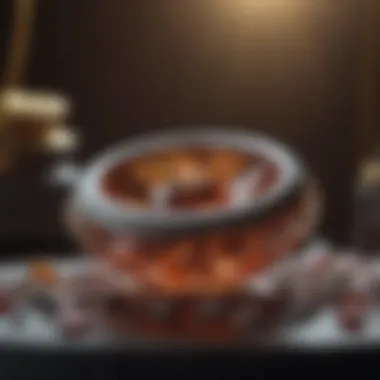

Impact of Automation on Gemstone Crafting
As we tread into the future, automation is set to play a pivotal role in gemstone crafting. Automated systems not only enhance productivity but also ensure a level of consistency that is hard to achieve through manual labor. For instance, robotic arms and automated polishing machines can operate continuously, producing exquisite pieces at a pace that meets today’s market demands.
However, the transition to automation brings its own set of considerations. While automation can free artisans from mundane tasks, there exists a palpable fear of losing the individual touch that comes with handcrafted jewellery. Many artisans value the connection they have with their creations, which might diminish if machines take over their roles entirely. Thus, the challenge is to find a harmonious balance where technology complements human finesse.
"The future of gemstone crafting hinges on our ability to blend tradition with technology, keeping the artistry alive while embracing advancements."
Adopting technology also means investing in training for jewellery makers. As equipment becomes more sophisticated, so too must the skills of those who operate them. The newer generation of artisans will need to become adept at managing and operating these complex machines.
Case Studies: Successful Artisans
In the vibrant world of gemstone crafting, the jeweller grinder plays a crucial role. The artisans who master this tool not only elevate their craft but also transform raw stones into coveted pieces of jewellery. This section dives into the lives and work of notable jewellers who have harnessed the power of grinding techniques and equipments effectively. By studying these successful artisans, readers can glean insights into their methods and philosophies, offering inspiration and practical knowledge for their own creative journeys.
Profiles of Notable Jewellery Makers
One cannot overlook the impact that specific artisans have had in the realm of gemstone crafting. Each one brings a unique blend of creativity and technical prowess, bridging the gap between functionality and artfulness in their pieces.
- Luca Rossetti: Renowned for his meticulous approach, Luca uses a combination of electric and manual grinding techniques. His signature style often incorporates intricate textures that enhance the natural beauty of the stones.
- Sofia Chen: A master of balancing modern technology with traditional craft, Sofia infuses her designs with organic shapes and asymmetry. She often employs diamond grinders for precision, elevating her pieces in contemporary jewellery markets.
- Jasmine Dubois: Known for her stunning use of colours, Jasmine relies heavily on her trusty manual grinders to achieve one-of-a-kind finishes. Her work celebrates the imperfections of natural stones, leaning into their raw beauty.
Each of these artisans shares a belief that grinding, while technical, is an art form in itself. Their stories reflect determination, innovation, and a love for the craft that can inspire both newcomers and seasoned professionals alike.
Techniques That Set Them Apart
The techniques employed by these successful jewellery makers not only define their brands but also offer key lessons in the jewellery industry. Here are some notable methods:
- Creative Use of Textures: Many artisans like Luca Rossetti focus on the textural qualities of a stone. This involves experimenting with different pressure and angles during grinding to unveil unique patterns, setting their pieces apart from mass-produced items.
- Mixing Traditional with Modern Approaches: Sofia Chen’s ability to blend old-school grinding methods with innovative technology is noteworthy. She often begins the process manually and transitions to electric grinders for finer details, showcasing a harmonious balance between tradition and modern efficiency.
- Colour Enhancement Techniques: Jasmine Dubois uses grinding not just for shaping but also for enhancing the natural colours in her gemstones. She carefully adjusts her grinding technique to bring out hues more vividly, thus making every piece more than just jewelry, but a canvas of artistic expression.
Artisans' techniques reveal a profound understanding of materials and an ability to adapt in a changing industry. By observing these methods, aspiring jewellery makers can develop their unique styles while appreciating the significance of grinding in their crafts.
"Crafting is a journey of discovery; every grind reveals what lies beneath the surface."
— Luca Rossetti
In sum, delving into the lives and techniques of successful jewellers offers invaluable insights. The stories and practices shared by these artisans illuminate how grinding is not merely a function but the very heart of jewellery making, enabling crafters to create extraordinary pieces that resonate. Through their lenses, one can appreciate the art and science behind the craft, engaging both the mind and spirit in the world of gemstone jewellery.
The Art and Craft of Gemstone Grinding
Gemstone grinding is not just about transforming rough stones into polished jewels; it’s an art that requires skill, precision, and an understanding of both the material being worked on and the tools being used. The role of a jewellery grinder goes beyond mere functionality—it's about creation that marries aesthetics with practicality. This section explores how artisans balance these elements, elevating their craft to new heights.
Balancing Functionality with Aesthetics
In the world of jewellery making, it’s crucial to find the sweet spot between utility and beauty. The grinders play a pivotal role in this balance. When grinding gemstones, a jeweler isn’t only focused on making the stone shine; they’re also considering the stone’s structure, its characteristics, and how it fits into the larger piece of jewellery.
- Tool Selection: Different grinding wheels serve diverse purposes. Whether it’s a diamond-coated wheel for hard stones like sapphires or a softer wheel for more delicate opals, the right tool can mean the difference between a gorgeous piece and a ruined one.
- Technique Matters: The method employed while grinding is equally important. A steady hand and an eye for detail ensure that the aesthetics of the stone are upheld. Too much pressure can ruin a gem, while too little won’t achieve a satisfactory polish. It’s all about understanding the material at hand.
- Artful Shapes: Grinders allow for the creation of unique shapes that enhance the stone's beauty. From classic round cuts to more unconventional designs, it’s the jeweller’s artistry that dictates how the final piece resonates with its audience.
Ultimately, the aim is to create a stunning piece that does justice to the stone's natural beauty while remaining functional and comfortable for wear. By merging functionality with aesthetics, artisans craft not just jewellery, but emotional connection.
Creating Unique Textures and Finishes
One of the joys of gemstone grinding is the ability to impart unique textures and finishes on the stones. This versatility opens up a world of creative possibilities. Here’s how this process unfolds:
- Surface Textures: Different grinding techniques create various surface textures. A jeweler might use a coarse grinder first to shape the gemstone, followed by finer wheels for a smooth finish. The layered textures can add depth and intrigue to the gemstone, making it more visually engaging.
- Finishing Touches: A glossy finish is often the goal; however, some jewelers go for a matte look or even a frosted effect. These distinct finishes can influence how light interacts with the stone, creating optical effects that catch the eye in unique ways.
- Personalization: Each gemstone can tell its own story with the right grinding approach. Customers today often seek bespoke pieces, and unique textures are a key component of that customization. Jewellers who can master these nuances can create pieces that stand apart in a crowded marketplace.
"Creating unique textures isn't just about aesthetics; it’s about breathing life into each stone, telling its story through craftsmanship."
In summary, the art of gemstone grinding encapsulates a delicate balance between functionality and aesthetic appeal. By investing time in honing these skills, a jewellery grinder not only enhances the beauty of the stone but also enriches the entire jewellery-making process. This nuanced craft allows artisans to create pieces that are both beautiful and meaningful.
End
In wrapping up our exploration of the role of a jewellery grinder in gemstone crafting, it's crucial to understand the multifaceted nature of this essential tool. A grinder is not just an accessory in the workshop; it is a cornerstone of the entire crafting process. Without it, achieving the meticulous precision that defines quality jewellery would be an arduous task.
Recap of Key Points
Let's revisit some of the important insights from our discussion:
- Types of Grinders: From electric to manual grinders, each type offers unique benefits tailored to different crafting styles and preferences.
- Techniques for Effective Grinding: Understanding speed and pressure plays a critical role in preserving the integrity of the gemstone while achieving the desired finish.
- Maintenance Practices: Regular upkeep of the grinding equipment is necessary for maintaining optimal performance and prolonging the lifespan of both tools and gemstones.
- Safety Protocols: The importance of protective gear cannot be overstated; safety must always be a priority when dealing with cutting and grinding tools.
- Innovation in Grinding Technology: As the industry progresses, advancements in grinding equipment and automation present new opportunities for improved efficiency and creativity.
The Ongoing Relevance of Grinding in Jewellery
The process of grinding gemstones isn't just a relic of old-world craftsmanship; it's a dynamic art form that continues to evolve. Today's jewellery makers combine tradition with modern technology to enhance the particulars of their work. Each grind can impact not just the quality but also the character of the piece. As craftsmen strive to set their work apart, the grinder remains a pivotal element in achieving uniqueness and artistry in every item of jewellery they create.
Furthermore, as new materials come into play and design trends change, understanding the role of the grinder in accommodating these shifts is vital for current and aspiring artisans.